What We Do
Consistent Production System
Based on the know-how we have accumulated since our establishment as a manufacturer. we have developed a consistent production system that gives our customers full satisfaction, from design to processing, molding, inspection, and with the most advanced cleanliness technology equivalent to Class 10000.
We have a full range of equipment including a 950-ton injection molding machine, a mold welding machine, a completely original large-capacity crusher, and a clean room for medical use to meet various requests.

Cutting model production in resin/metal
Plastic product design, precision model making, vacuum casting, vacuum molding, etc.
One-stop service from resin mold design to manufacturing
Designing and manufacturing of plastic molds in Japan and overseas. Our thorough flow analysis promises high quality molding products.
Small lot/multi-model, coloring, in any size
Regardless of the size of the product, we have production systems in Japan and overseas, including logistics.
Leave the secondary processing to the experts
Silk printing / pad printing / hot stamping
Paint, plating, hydraulic transfer
Ultrasonic welding / Hot plate welding
Simple ASSY and various other secondary processing.
Partnering
We have collaborated with a number of partner companies.
Please feel free to contact us for a variety of requests such as urethane foam injection processing.
Repellet processing
We re-pellet waste plastics generated in the manufacturing of plastic products, including defective products and losses.
We re-pellet end-user materials, defective products, and discarded materials and products so that they can be reused without wasting raw materials.
Please feel free to contact us for more information.

Repelleting process flow
Shipping
Please send the raw materials and products to us.
We will confirm the resin name, grade, color, and quantity.
We have a completely original crushing equipment that can be used for various sizes.

Tumbler
We use a powerful crusher to crush ordinary products as well as sheets. Even if the crushed material is the same lot, the moisture absorption and the shape of the crushed material are different between the crushed material at the beginning and the crushed material at the end.
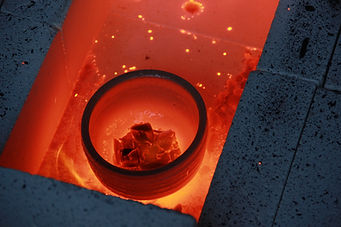
Heating and melting
The product is heated and melted in our original extruder. We check the melting condition of the resin, and finally judges the condition of the crushed material and sets the best temperature conditions for processing.

Cutting & Metal Detectors
The strands from the extruder are cut into pellets.
The detection capacity is 0.3 mm for Fe, 0.3 mm for SUS304, and it is put through a metal detector before bagging to remove all metals, both magnetic and non-magnetic, even if they are contained in the pellet.

Weighing & shipping
The pellets are weighed and measured, carefully packed in bags, and delivered to the designated place on the desired delivery date.
Medical waste box/pail
We manufacture medical waste boxes in a wide variety of sizes.
They meet all medical level regulations and can be used in a wide range of applications, not only for home use but also in restaurants and medical settings.
Product examples - Medical waste boxes

PNH Series
2L compact size
Chemical splash prevention cover
Four handles make it easy to carry around.
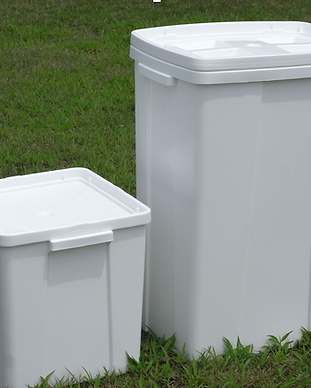
PN-20/50 series
40% reduction in waste when stacking the body
Hard to fall over
For the entire bottom of the C/V for transport R
We also manufacture a variety of other sizes and types of medical and medical waste boxes.
Please feel free to contact us for more details.